Hq Service Manual
Mods.dk - Instruction, users and service manuals for Hammarlund Main Menu Manuals for Hammarlund This is the manuals page for Hammarlund. In this page you find schematic, users and instructions manuals, service manuals, technical supplement, leaf leads and other good stuff. If you have some stuff that not is listed here you can donate this.
Note that there is a limit to the number of files you can download. And when you click on the file or icon it will count as a download. If you can't find a manual please do not contact us, all the manuals we have are online.
675 Kbytes 699 Kbytes 731 Kbytes 755 Kbytes 986 Kbytes 1.155 Kbytes 1.132 Kbytes 4.561 Kbytes 392 Kbytes 1.003 Kbytes 1.863 Kbytes 398 Kbytes 1.529 Kbytes 2.127 Kbytes 772 Kbytes 1.560 Kbytes 656 Kbytes 635 Kbytes 5.511 Kbytes 2.256 Kbytes 994 Kbytes 4.127 Kbytes 967 Kbytes 2.432 Kbytes 3.046 Kbytes 195 Kbytes 1.707 Kbytes 6.067 Kbytes 1.482 Kbytes 13.932 Kbytes 717 Kbytes 10.127 Kbytes 31.519 Kbytes 167 Kbytes 1.651 Kbytes 21.451 Kbytes 8.523 Kbytes 834 Kbytes 6.238 Kbytes 47.389 Kbytes 316 Kbytes Total: 193.277 KBytes This is all the manuals for Hammarlund. If you want to see manuals from other manufactories you can click on the manufactory menu in the left side. You can also that mods.dk have manuals, schematics or other files from. © Copyright mods.dk 1996 - 2018.
. Service and Troubleshooting Manual -12/20/06- © Handi Quilter, LLC. Table of Contents About the HQ Sixteen About the manual Service Manual General Rules General Specifications (I) Lubrication Specifications (II) Adjustments: Page Lubrication Instructions.0.1 – 0.4 General Observation of Front Frame Cover, Mast and Hand Wheel.1.0 – 1.1 Removal of Front Cover.2.0.-2.2 Securing Flats and Screws.3.0 –. If you need help in locating these tools for purchase, please contact Handi Quilter, LLC Handi Quilter’s Customer Service technical staff is available for assistance and advice during normal business hours. For additional help in technical training, we refer you to the training schedule at the Corporate Office in Bountiful, Utah. General Specifications Dimensions: (210 X 410 mm) 8.25” X 16.00”) Sewing Speed: (Min 150spm, Max, 1500 spm) Needle System: 134R (135 X 7) Needle Sizes, (recommended): 14/90 - 19/120 Hook System: (Rotary, custom made, Cerliani, Type FA, Vertical, M Bobbin) Bobbin Type: Aluminum, Class M Bobbin Case. Lubrication Specifications Lubricant type Machine Components Kluber, Constant OY68 All main bearings Kluber, Mikrozella G 8 OY Main bearing reservoirs Kluber, GLY 2100 Take-up articulating link Kluber, NCA 15, Isoflex Take-up caged Needle bearings Kluber, GLY 151, Polylub Transmission gears Conoco, Hydroclear R&O 32 Hook race or similar white oil, i.e.
Lubrication Lube Kit Part# 388-000-004 The HQ Sixteen lubricating schedule should be followed every year up to every two years to insure top mechanical performance. This is a two-part lubrication system. Lube #1 (Red) at points shown first.
Apply the reservoir gel Lube #2 (Blue) on the side of the bearing and or under the bearing retainer straps. Lube #4 (Green) Kluber Isoflex NCA-15, the belt idler wheel needle bearings. Lube #1 (Red) Kluber Constant OY 68, the transmission shaft bearings followed by Lube #2 (Blue) Mikrozella G8 0Y, as before stated. Lube #1 Red Lube #2 Blue Apply Lube #5 (Orange) Kluber GLY 151 on the Delrin gear to provide a dampening lubricant for. Lubrication Chart for HQ Sixteen (2005 Improved Version) Several improvements were made to the HQ Sixteen machine in 2005. Some of the improvements are the introduction of a new head-frame, presser bar guide, and transmission gearing.
Please observe the lubrication instructions for these new features. All other lubrication in the previous lubrication chart should be observed as noted. #1 (Red) OY 68 One drop on each bearing bushing. #2 (Blue) Mikrozella G8 0Y Add a dab to the end of each bearing bushing. #5 (Orange) GLY 151 Add a small dab to reduce gear noise.
General Observation of the Front Frame Cover, Mast, and Hand wheel The following observations, accompanied by necessary adjustments, will ensure trouble-free thread passage. Failure at any of these points will significantly affect thread tension. Tools required: (2mm, 2.5mm handle allen, 8mm open end wrench) Check: 1.
Check the top tension assembly for the following:. A gap of 1.0mm to 1.5mm exists between the frame boss and the back disk of the tension assembly, see figure 1.4. If a correction is necessary: loosen screw.
(2mm handle allen), adjust the gap between the front cover and the rear tension disk, and retighten screw. Removal of the Front Cover Tools Required: 2mm, 3mm, 4mm handle allen, 4mm L allen, #3 fillister screwdriver, and #2 phillips screwdriver.
Loosen the set screw A in Figure 2.1, rotate the thread guide 3 to allow access to the frame screw, then re-snug. (2mm handle allen tool) Figure 2.1 2. Remove the needle plate. (#3 fillister screwdriver) Figure 2.5 6. Remove the 5 frame screws D in Figure 2.6 Note: the fifth screw is behind the C-print removed in step 4. (4mm handle allen – may need 4mm L allen tool to break loose screws) Figure 2.6 7.
Hq Avante Service Manual
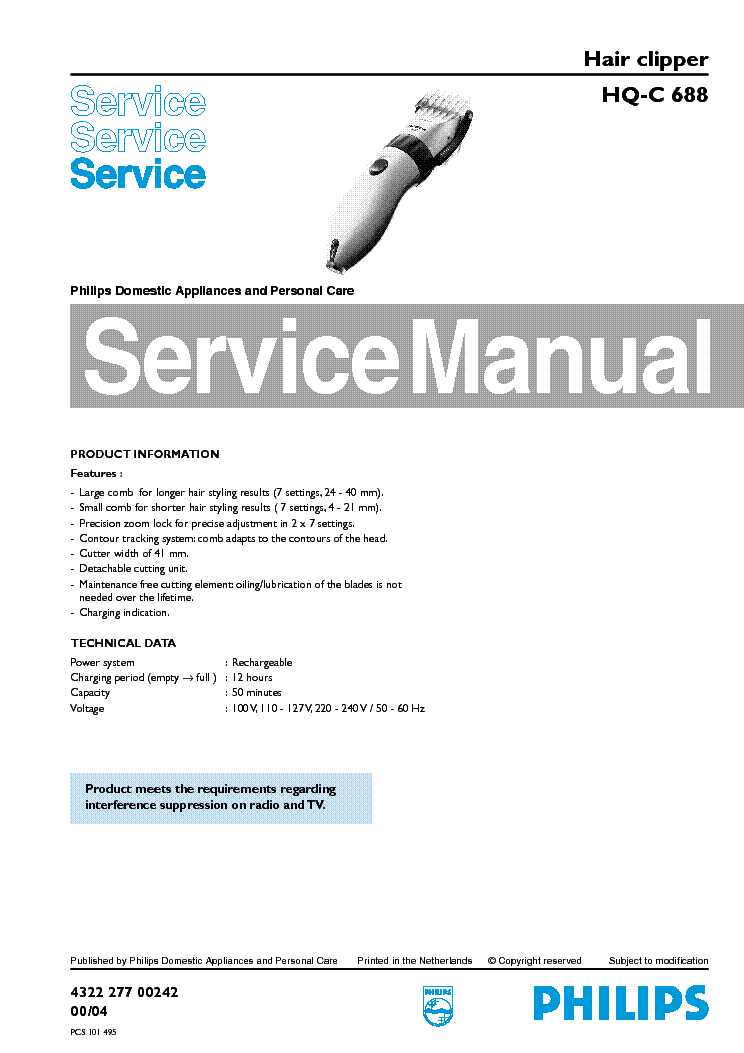
Replacement of cover: Replace the front cover in the reverse order that it was disassembled. Note: See torque specifications chart in the specification section for torque values. C-Print/Pod Cables P-Print/Pod Cables Connections CAUTION DANGER OF ELECTRICAL SHOCK – DANGEROUS VOLTAGES Do not plug main power or run the sewing machine with the p-pod off of the machine and or open so that human body part comes in contact with electrical energy.
Checking and Securing Flats and Screws The HQ Sixteen has been designed using flats and special screws so that loop lift timing cannot slip. Tools required: (2.0 and 2.5mm handle allen) Pitman Crank Check the following locations, making sure that the first screw of a timed component has been fixed firmly on the Pitman respective flats on shafts. Checking and Securing Flats and Screws (Continued) Hand-wheel Handwheel screw – inside frame (3mm handle allen ) Secondary Drive Drive pulley screws (2.5mm handle allen) Pulley Figure 3.5 Transmission gear and pulley screws – (2.5mm handle allen) Figure 3.6 Hookshaft gear screws - (2.5mm handle allen) Figure 3.7. Axial Play Check and Adjustment Axial or end play on shafting can result in noise, wear, and faulty sewing. Tools required: (2, and 2.5mm handle allen) Check: 1. Check the arm-shaft by pushing and pulling on the hand wheel.
See Figure 4.1. If a correction is necessary:. Adjusting the Base Plate feet and Rollers Tools required: (5mm handle allen) Check: 1. The Base Plate must be adjusted so that the rubber feet will sit flat on a planed surface. If a correction is necessary, 0.012” shim washers may be used as shown in Figures 5.1 and 5.2. Adjusting the Motor Belt Tension NOTE: The motor belt tension need not be tightened as tightly as the main timing belt (see 6 c.) Check the belt tension for tautness by pressing it with the index finger (see Figure 6.1). Proper belt tension provides for some belt flexibility under light finger pressure, but should not be so tight as to bind the machine.
Adjusting Transmission Gear Lash (play) Check the transmission gear lash, between the metal transmission gear and the delrin hook shaft gear. NOTE: Do not adjust this unless you are sure it needs adjusting. This will affect the timing of the machine.
There should be little or no lash between the two gears. Adjusting the Timing Belt Tension Check the timing belt for tautness by holding the transmission pulley and rocking the hand wheel. You should not be able to feel play between the belt teeth and the transmission timing pulley teeth. NOTE: if you tighten the belt too much you will create a bind or extra noise in the machine. Adjusting the Presser Bar Height Version A (Older Machines) (Tools required: 2mm handle allen, 2mm L allen, and 1.500” height gauge) Check: This adjustment is made with the front frame cover off. When the needle bar is at its lowest position the presser bar must be 1.5”.

Hq Avante Service Manual
Adjusting the Presser Bar Height Version B (Newer Machines) (Tools required: 3 mm handle allen, 0. 5mm feeler gauge) Check: When the needle bar is in its lowest position, the sewing foot should be no higher than 0.5mm above the Figure 13.1 needle plate as shown in Figure 7.3. Needle Position, Check, & Adjustment Tools required: 2mm, 3mm handle allen The needle position adjustment is the most important of all adjustments in the machine. Needle Position provides the foundation for which all other settings are made. Once the needle position has been completed, great care must be maintained to keep this setting. Adjustment of the Loop Lift and Needle Distance “Loop Lift” is a universal hook and timing term for all lock stitch sewing machines. When the needle lifts a specified distance from the BDC (bottom dead center), the hook point is set to coincide with the needle as shown in figures 9.4 and 9.5 Tools required: (loop lift clamp, part no.
9 Adjustment of the Loop Lift and Needle Distance Continued Rotating basket down - Note: With the bobbin case basket in the normal position, the basket needle guard deflects the needle and makes it difficult to accurately adjust the needle distance between the hook point and the back of the needle scarf. Adjusting the Needle Height Tools required: (#2 or #3 Fillister screwdriver x 150mm) Check: This adjustment must be completed with the front frame cover on.
Important note: shown with cover off for illustration purposes only! The needle height must be set so that when viewed from behind as shown, the hook point is flush with right side of the needle. Adjustment of the Stop Finger Tools required: (2.5mm handle allen) Check: The engagement of the Stop Finger and throat of the bobbin case support basket must have a clearance of 0.8mm to 1.0mm. (This clearance ensures that adequate space exists for thread escapement during the sewing process).
Adjusting the Needle Height with Cylinder Tool Note: The adjustment with the cylinder tool Tools required: (#2 or #3 Fillister requires the hook be removed, so loop lift and screwdriver x 150mm, Needle Height Cylinder tool) needle distance will have to be reset afterwards. Check: Turn the handwheel in the direction of motion until the hook point becomes even with the right side of the needle as shown in (Fig 12.1). Bring the needle to the lowest point by 4.
Wep Hq 2100 Service Manual
Slide the Cylinder tool gently against rotating the handwheel. (Fig 12.4) the needle.
Astra 2016 owners manual. (Fig 12.5) Figure 12.4 Figure 12.5. Sight through the needle eye and compare the upper and lower levels of the eye with the Cylinder tool groove.